How do you manage your maintenance schedule? With a planned maintenance approach there’s the possibility to stop costly issues before they start.
Equipment downtime can lead to significant financial losses and disrupted workflows. To mitigate these risks, businesses are increasingly relying on planned maintenance strategies. A critical component of planned maintenance is calibration, which ensures that equipment operates within its specified parameters, enhancing both performance and lifespan.
What is Planned Maintenance?
Planned maintenance, also known as scheduled or preventive maintenance, involves regular, pre-planned servicing of equipment to prevent unexpected failures. This proactive approach aims to address potential issues before they escalate into costly breakdowns. Planned maintenance typically includes tasks such as inspections, part replacements, lubrication, cleaning, and adjustments.
The Benefits of Planned Maintenance
Let’s be clear here, the benefits of planned or preventative maintenance (whichever phrase you choose to use) are numerous and widely known. Here’s a few:
- Reduced Downtime: Regular maintenance reduces the likelihood of unexpected equipment failures, keeping operations running smoothly.
- Cost Savings: By preventing major breakdowns, businesses save on emergency repair costs and potential production losses.
- Extended Equipment Lifespan: Proper maintenance extends the life of equipment, maximising the return on investment.
- Improved Safety: Regular checks and maintenance ensure that equipment is safe to use, reducing the risk of accidents.
- Compliance: Adhering to maintenance schedules helps in meeting regulatory and industry standards.
The HSE talks about the maintenance of plant and equipment as being very important; they say:
‘An effective maintenance programme will make plant and equipment more reliable. Fewer breakdowns will mean less dangerous contact with machinery is required, as well as having the cost benefits of better productivity and efficiency.
Additional hazards can occur when machinery becomes unreliable and develops faults. Maintenance allows these faults to be diagnosed early to manage any risks.
However, maintenance needs to be correctly planned and carried out. Unsafe maintenance has caused many fatalities and serious injuries, either during the maintenance or to those using the badly maintained or wrongly maintained/repaired equipment.’
The Role of Calibration in Planned Maintenance
Calibration is the process of adjusting and verifying the accuracy of equipment by comparing its measurements to a known standard. This is especially crucial in industries where precision is vital, such as manufacturing, pharmaceuticals, rail, aerospace, and food production.
Here’s how calibration fits into the planned maintenance strategy:
- Ensuring Accuracy: Calibration ensures that instruments and equipment provide accurate readings. Inaccurate measurements can lead to poor product quality, increased waste, and safety hazards.
- Consistent Performance: Regular calibration maintains the consistency of equipment performance, ensuring that operations run smoothly and efficiently.
- Identifying Wear and Tear: Calibration can reveal subtle changes in equipment performance, indicating wear and tear that might not be visible during routine inspections. This allows for timely interventions.
- Compliance and Certification: Many industries require regular calibration to comply with regulatory standards. Keeping calibration records helps in audits and certification processes. Here at CoMech we provide TrackRecordPro as the system for outstanding traceability when it comes to your calibration of assets.
- Optimising Maintenance Schedules: Data from calibration can be used to fine-tune maintenance schedules. If certain equipment consistently drifts out of calibration, it may need more frequent maintenance or adjustment.
Implementing Calibration in Planned Maintenance Schedules
To effectively integrate calibration into a planned maintenance program, businesses should consider the following steps:
- Inventory or Asset Management: Maintain a detailed inventory of all equipment requiring calibration, including specifications and calibration intervals. As before, CoMech can support you with this either by compiling your asset list or managing it via our system TrackRecordPro which provides certification, failure reports, reminder dates, and other useful information.
- Develop a Schedule: Establish a calibration schedule based on manufacturer recommendations, industry standards, and historical performance data. If in doubt talk to our technical team; there is very little kit they don’t have knowledge on so will be able to advise how regularly calibration will be needed to keep everything in optimal condition.
- Use of Technology: Leverage software solutions for tracking calibration schedules, maintaining records, and generating reports. This can help in ensuring that no equipment is overlooked.
- Partner with Experts: If you are consider partnering with accredited calibration service providers who have the expertise and equipment to perform precise calibrations then CoMech could be the turnkey calibration service provider for you. We have an extensive UKAS scope which covers both our Derby based laboratories and our onsite engineers who come to your site as and when needed.
- Continuous Monitoring: Implement a system for continuous monitoring and feedback. Analysing calibration data can help in identifying trends and potential issues before they affect operations.
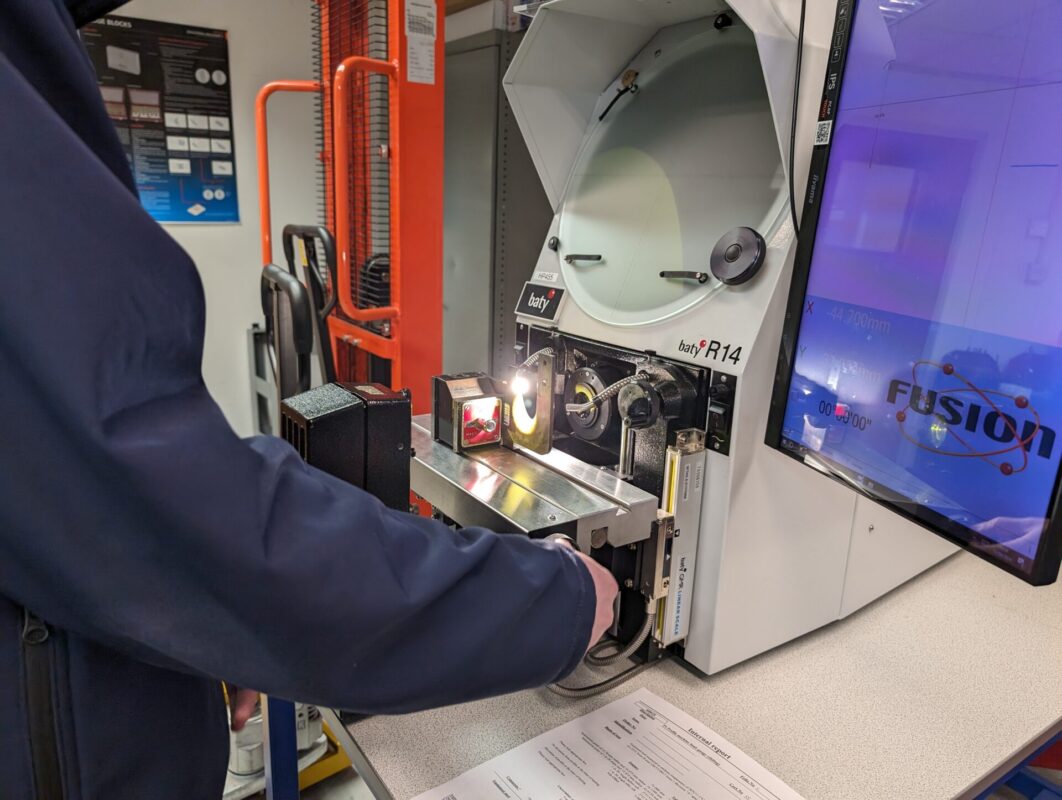
Incorporating calibration into a planned maintenance strategy is essential for maintaining the accuracy, efficiency, and longevity of equipment. By ensuring that instruments are properly calibrated, businesses can avoid costly downtimes, enhance safety, and achieve regulatory compliance. The integration of regular calibration into maintenance routines ultimately leads to smoother operations, better product quality, and increased profitability.
Adopting a comprehensive approach to planned maintenance that includes calibration not only protects investments in equipment but also contributes to the overall operational excellence of an organisation. Investing time and resources into this proactive strategy is a wise decision that pays off in the long run.